Firing Up PTFI Smelter in Manyar Is More Than Flipping a Switch
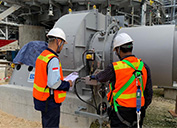
May 29, 2024 - Firing up one of the largest copper smelters in the world is not just a matter of flipping a switch. It is a process that was years in the planning and will take months to execute.
Critical components of PT Freeport Indonesia’s smelter complex in Manyar near Surabaya, Indonesia, are undergoing commissioning, the process of bringing them into service after construction is complete and equipment is installed. The flash smelting furnace, the first furnace in the copper refining process, will begin heating up about June, although first cathode is not expected to be produced until about October.
There is no single defining moment that marks the commissioning of the copper smelter, said Clint Crotts, Director-Project Commissioning, who heads Freeport-McMoRan’s commissioning team. Rather, there is a series of important milestones as individual components of the smelter complex become operational and copper concentrate begins to flow.
The project is so vital to both Freeport and the Indonesian economy that there will be an official day recognizing the accomplishment, probably sometime in the fall. But it will represent the culmination of thousands of individual achievements to help ensure that the hundreds of complex components work in harmony.
To make the smelter operational, every piece of equipment must be checked and tested to make sure it works as a stand-alone part. It also must be synchronized with the thousands of other components needed to take copper concentrate from the new dock where it will arrive on ships from the company’s mining complex in Papua, through the smelting and converting furnaces and out of the new electrorefinery as copper cathode.
“It’s not push the button, start the plant,” Crotts said. “It’s a sequence of starting the different components of the plant. We have to fine tune the systems, and make sure that every part of the plant is working within the design criteria.”
Expansive project
The smelter project is far more than the smelter itself, said H-D Garz, Executive Vice President-Corporate Planning and Business Strategy at PTFI. The 272-acre complex includes a copper electrorefinery for producing cathode, a precious metals refinery to recover other metals like gold and silver, a gas cleaning and acid plant, a desalination plant to treat sea water, an effluent treatment plant to process water used in the operation, surface water and traditional sewage treatment plants, a web of conveyors and storage beds, and dozens of warehouses, workshops, support buildings, power transformers and other facilities.
All those components need to work in harmony for the smelter to function, Garz said. The primary source of copper concentrate is the PTFI mining complex near Timika, Papua, more than 1,700 miles away.
When in full operation, the smelter will have a capacity of processing 1.7 million metric tons of copper concentrate annually, about 70 percent more than Freeport’s smelter in Miami, Ariz. The electrorefinery will be able to produce 480,000 tons of copper per year.
It took years to plan not only what would be needed but the sequence the various components will come online to support the smelter operation.
Anything not available had to be built.
Even firing up the smelter furnace itself is a complex process, Garz said. Built of special refractory brick and mortar, it needs to be “cured” under high heat for a period before it can be set to its standard operating temperature of about 2,300 degrees Fahrenheit.
During the commissioning process, the corporate commissioning team will conduct detailed inspections and testing of all equipment to make sure it was constructed to specifications and operates as intended. There is a checklist with hundreds of individual items that will be inspected and tested to make sure they are working and integrated with the overall system.
Much of the work is being done by the people who will become full-time operations employees at the smelter complex.
Sequencing is critical, Garz said. For instance, the gas cleaning and acid plant needs to be tested, ready and operational to capture the combustion gases from the smelting process and convert these to sulfuric acid, ready to be stored and shipped in large quantities before smelting can begin. Otherwise, the acid would back up the operation and force a shutdown.
“You can’t start the furnace without being able to handle what comes off the furnace,” Garz said. “So, there is phasing and sequencing that you have to do. Once you start you really don’t want to have to stop.”
Photos (left to right): Workers at Freeport’s new Manyar smelter complex in Indonesia are ensuring thousands of components are tested, functioning and synchronized as part of the commissioning process; Before the new Manyar smelter becomes operational, all related components in the complex must be checked. These include a new electrorefinery, a precious metals refinery, a gas cleaning and acid plant and a seawater desalination plant; Most of the people involved in the commissioning of the new Manyar smelter will be full-time employees once it is in operation.
SOCIAL
RECOGNITION